Maintaining your truck fleet in top condition isn't complicated. It all comes down to regular maintenance checks, spotting problems before they worsen, monitoring fleet health, and implementing prevention-focused strategies. Regular inspections and repairs guarantee minimal downtime, enhanced productivity, and protection. Expert guidance from experienced technicians can help you master fleet maintenance through the effective use of technology, detailed record-keeping, and skilled team members. Go ahead, immerse yourself in this complete guide to fleet maintenance and discover cost-effective operations. There's plenty to learn and master!
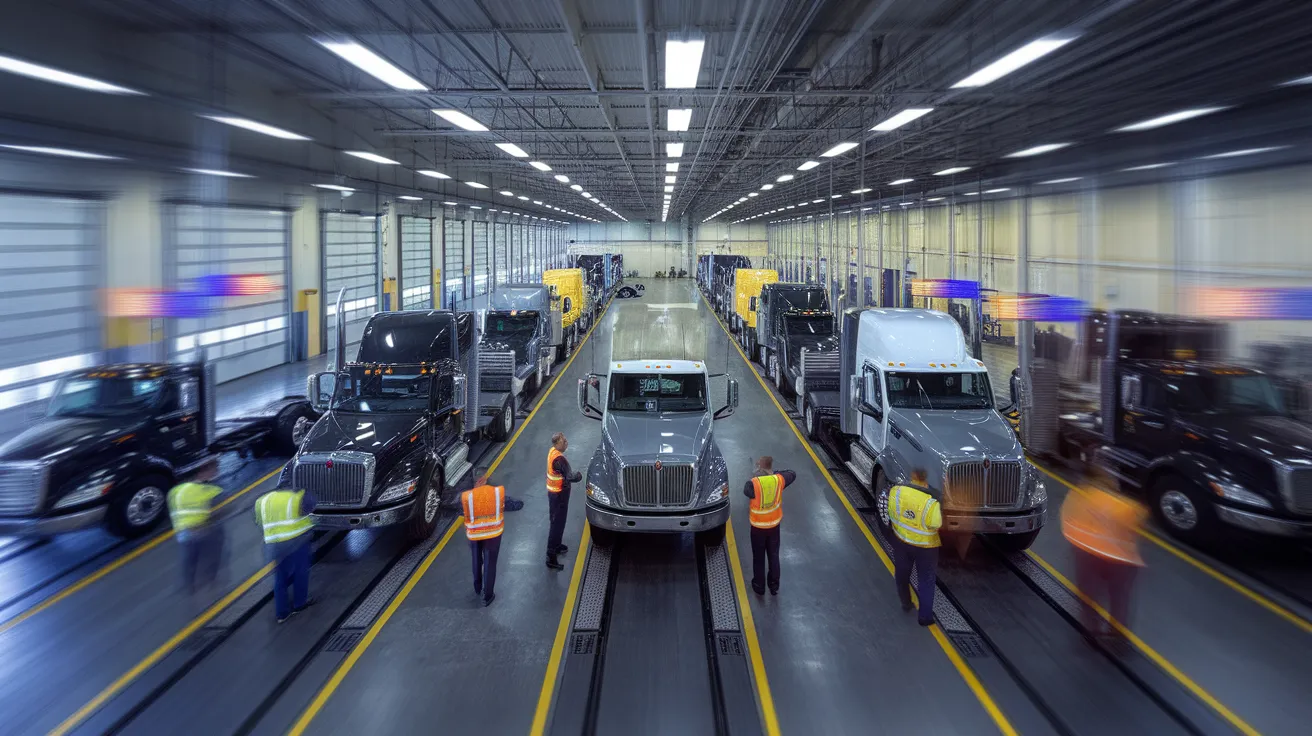
Key Takeaways
Understanding the Importance of Scheduled Fleet and Truck Service
Although it might seem daunting, understanding proper fleet and truck maintenance is vital for any successful business. You'll find the advantages of maintenance far outweigh the time and effort invested. Regular checks and servicing can significantly extend your vehicles' longevity, preventing expensive replacements. Furthermore, there's an undeniable connection between well-maintained trucks and enhanced fuel performance. This translates to decreased fuel spending, improving your total operational efficiency. Furthermore, routine servicing can help identify small problems before they become serious problems, preventing costly repairs in the future. So, don't underestimate the value of regular upkeep; it can be a real game-changer for your company's profitability.
Examining Critical Aspects of a Effective Maintenance Program
To ensure your fleet's efficiency and durability, it's essential to pinpoint the vital elements of a well-designed maintenance program. You'll have to grasp the basic principles of maintenance, assess the status of your fleet consistently, and establish preventive measures proactively. With these implemented, you're positioned to minimizing downtime and enhancing productivity.
Core System Maintenance Features
If website you aim to improve your fleet's productivity and longevity, establishing a solid maintenance program is essential. Critical elements of the program include scheduled inspections, routine servicing, and anticipatory repairs. Every component is instrumental in minimizing expensive failures and decreasing downtime. While the rewards of a maintenance program are significant, it's important to address the obstacles to implementation. These may include resource constraints and employee pushback. Yet, with careful preparation, transparent dialogue, and commitment to education, these barriers can be surmounted. Don't forget that an effective maintenance program doesn't just resolve issues; it averts them. It's an commitment in your fleet's longevity – and it's one that will yield significant returns.
Equipment Status Tracking
As you explore the specifics of a effective maintenance program, understanding the importance of fleet condition monitoring becomes paramount. It goes beyond keeping your vehicles running, it's about optimizing fleet performance. Fleet monitoring systems offer a complete view of your fleet's condition, allowing you to identify potential issues prior to escalation.
Such tracking solutions measure important indicators like fuel efficiency, tire conditions, engine performance, and more. By utilizing this data, you're not just guaranteeing the durability of your fleet but also saving on unnecessary repair costs. Keep in mind proactive identification is essential in fleet management. Therefore, invest in reliable monitoring solutions and stay ahead of the curve. Don't merely address problems, anticipate them. Monitor your fleet's status regularly and your enterprise will run smoothly.
Implementing Preventive Measures
While keeping tabs on your fleet's condition is essential, putting preventive strategies in place is just as crucial to maintain a robust maintenance program. You need to identify potential problems before they transform into major repairs and equipment downtime. Let's explore preventive maintenance approaches.
An important strategy is establishing a comprehensive maintenance checklist. This checklist should outline all required checks, maintenance procedures, and parts renewal. Routine engine monitoring, tire servicing, and oil changes are essential. Make sure to include smaller components like wiper blades, illumination, and filters.
Your maintenance plan needs to include a schedule for every maintenance item. Adhering to this plan ensures that your fleet maintains optimal performance. Keep in mind, preventative care saves costs, time, and troubles in the long run.
Key Maintenance Tasks for Fleet and Truck Upkeep
To ensure your vehicles continue to be in optimal condition, you need to prioritize regular maintenance checks. These inspections encompass regular service evaluations and essential system reviews. By following these vital procedures, you'll extend your fleet's durability, optimize operational efficiency, and ultimately, reduce major repair expenses.
Regular Maintenance Inspections
Regular maintenance inspections serve as your strongest line of defense from unplanned vehicle and fleet malfunctions. These inspections offer you the ability to identify and resolve issues before they escalate into major repairs or hazardous situations. One of the primary benefits of routine maintenance is the reduction of operational delays, which can substantially influence your company's productivity and bottom line.
Critical Component Checks
Building on the importance of scheduled maintenance inspections, let's examine the specific essential component checks that ought to be performed regularly to ensure optimal truck and fleet performance. Start with the brake system – verify all components are operating correctly, from brake pads to fluid levels, and checking for leaks. When overlooked, brakes might fail, leading to serious incidents. Checking tire pressure is equally crucial. Insufficient pressure raises fuel consumption and tire wear, while overinflation can cause a blowout. Invest in a quality pressure gauge for accurate readings. Remember tires should be cold during checks for optimal results. Consistently conducting these important checks can save you from costly repairs and potential accidents. Maintain safety on the road.
Fleet Efficiency: Preventative Maintenance Best Practices
While overseeing a fleet, it's vital that you prioritize preventative maintenance to guarantee peak efficiency. Setting up a comprehensive preventative scheduling system is crucial. This prevents unnecessary wear and tear, and lowers the chances of unscheduled downtime. You should schedule regular checks and servicing based on mileage, time, engine hours, or fuel used. Keep in mind each vehicle is different and may require a personalized approach.
Training in maintenance is a crucial approach to secure peak efficiency. Provide your staff with the necessary skills to spot potential issues before they escalate. This saves both time and effort but also lowers operational costs. The integration of maintenance training and preventative scheduling will create a highly effective and reliable fleet. Prevention is always better than cure.
Essential Tips for Truck and Fleet Maintenance and Recovery
Even though vehicle fleet repair and restoration might appear challenging, grasping the fundamentals makes it easier. The first thing you should do should be to learn about different maintenance methods. This understanding will enable you to diagnose concerns swiftly and accurately. Following this, prioritize repair tasks based on the extent of repairs needed and the vehicle's role in your operation. Frequently check all units for potential issues and tackle them quickly to prevent further damage. Don't forget, renovation isn't simply problem-solving, it's focused on enhancing the truck's performance and lifespan. Finally, always use high-quality parts for repairs; they'll last longer and perform better. Keep these tips in mind, and you'll handle fleet maintenance and renovation effectively.
Harnessing Sector Developments for Advanced Fleet Maintenance
To maintain a competitive edge in the trucking industry, it's essential to harness innovative solutions for advanced fleet maintenance. New technologies are rapidly changing the maintenance landscape. Implement data analytics to analyze your fleet's performance and predict problems before they occur.
State-of-the-art monitoring systems keep track of engine performance and health, fuel efficiency, and operator performance. Utilize this valuable information to schedule preventive maintenance, helping reduce expensive downtime.
Always prioritize software updates. These improvements generally provide important updates and fixes that boost your fleet's performance and safety. Note that managing your vehicles isn't limited to routine maintenance. You're managing in a tech-focused period, and keeping up with sector developments will support your vehicles' longevity and revenue generation. By utilizing proper processes, you can lower expenses and effort, and safeguard human life.
Questions & Answers
What Qualifications Are Required for an Expert Vehicle Fleet Mechanic?
You'll need an official certification, satisfying the requirements of an established mechanic institution. Moreover, you must pass a thorough skill assessment, proving your expertise in different areas of fleet maintenance and repair. Experience counts too!
What's the Right Time to Replace Fleet Vehicle Tires?
Just like the seasonal changes, you need to examine your fleet's tire tread on a consistent basis. However, it's generally recommended to install new tires every 3 to 6 years, according to driving conditions and frequency of use.
What Are the Warning Signs of Truck Engine Problems?
You can identify engine issues in trucks through symptoms like abnormal engine noises and reduced fuel economy. Additional indicators are heavy smoke emissions, engine oil drips, or possibly an illuminated check engine light that persists.
How Does Technology Impact Truck and Fleet Maintenance?
Technology plays a vital role in optimizing truck maintenance. Telemetry systems deliver real-time data, while analytical tools forecast issues before they occur. You'll experience minimized maintenance delays, enhanced security and as a result, reduced expenses. It's revolutionary.
How Do Maintenance Needs Vary Across Fleet Vehicle Types?
Various vehicles need unique maintenance schedules. One must account for the intended use, carrying capacity, and driving conditions, as these elements greatly influence required servicing. Be sure to customize maintenance according to the vehicle category.
Closing Remarks
Ultimately, the key is maintaining optimal fleet performance, right? Consistent upkeep isn't optional, it's a must. By recognizing critical parts, carrying out systematic evaluations, using preventative strategies, and leveraging technological advances, you're doing more than basic maintenance, you're crafting an efficient operation. And don't forget, fleet servicing isn't a problem, it's a chance for improvement. Maintain your dedication, and you'll see your fleet's productivity, consistency, and lifespan soar to new peaks.